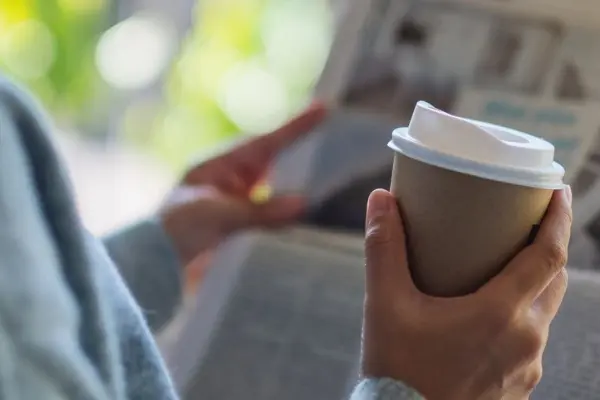
Aktualne informacje
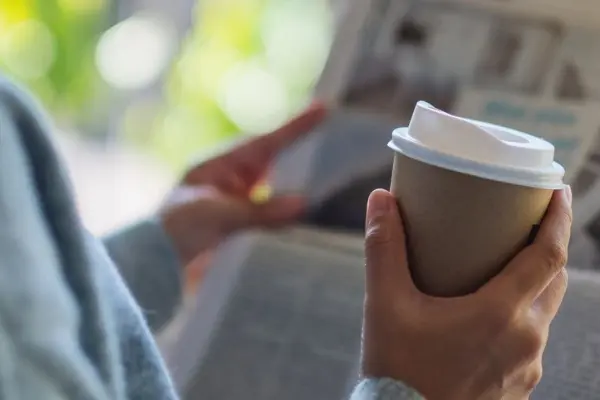
Aktualne informacje
Aktualności
Inwestycje w przyszłościowe obszary, takie jak elektromobilność, zrównoważony rozwój, cyberbezpieczeństwo i sztuczna inteligencja, umocniły pozycję firmy jako lidera nowoczesnych rozwiązań dla globalnego rynku.
Czytaj więcej
Bezpieczny i zrównoważony świat? To możliwe! Przeczytaj o tym w artykułach naszych międzynarodowych ekspertów.
Czytaj więcej